BENEFITS
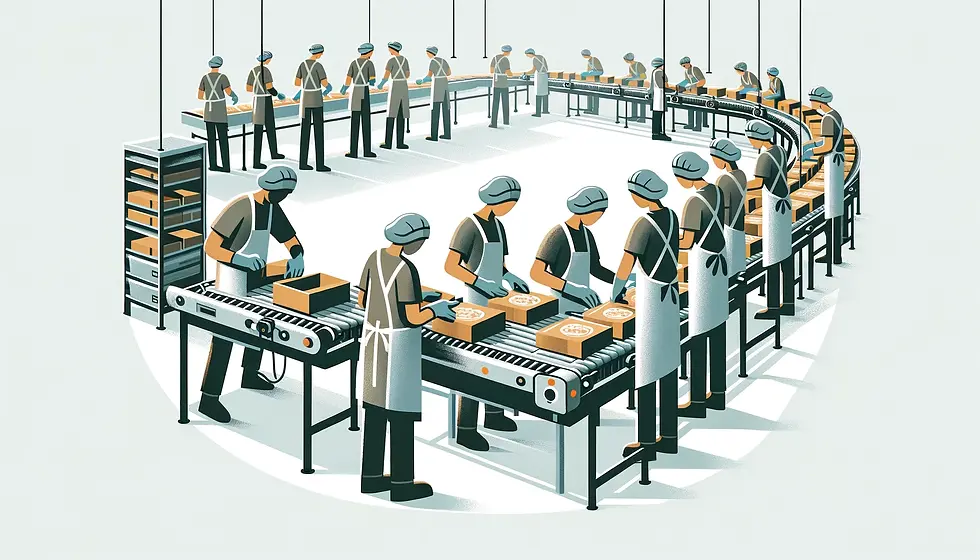.webp)
Precise Line Planning for Kitting Operations
Struggling with workload balance and efficiency in your kitting lines?
Discover a solution that enhances precision, safety, and quality of every meal kit or packing process.
Why Choose Us?
➤ Optimised Operations: Tailored solutions to boost efficiency, safety, and quality of kitting operations.
➤ Consistent Throughput: Achieve reliable, high-performance results with expertly balanced lines
➤ Reduced Errors: Minimise mistakes and improve accuracy in packing processes.
➤ Enhanced Safety: Create a safer workplace with intelligent workload management and proper item placement.
.webp)
Maximise Throughput
While increasing throughput may seem attractive, it's crucial to recognize that optimal labour efficiency requires a nuanced workload distribution to avoid more packers than the absolute minimum required to achieve a target throughput level.
Our solution strategically allocates ingredients for each recipe to racks and stations, ensuring that the workload is evenly distributed among packers, regardless of the recipe’s unique demands. This guarantees a balanced workload for each packer throughout the entire production, and ensures that only the necessary number of packers is used to achieve the target throughput.
Furthermore, our solution strategically assigns recipes to kitting lines to maximise the total shop floor throughput without assigning too much work to any kitting line to avoid creating a bottleneck for subsequent processes or missing production deadlines.
Minimised Changeovers
While increased throughput is primarily achieved by minimising idle time for each packer on a line, in other words improving individual packer efficiency, the overall shop floor efficiency can further benefit from reduced idle time during changeover and replenishment activities.
Our solution intelligently allocates common ingredients across different recipes to the same locations, ensuring that workload balance between stations is maintained, while also reducing changeover time by minimising the number of ingredients that need to be replaced.
Improved Production Quality
Proper packing practices, such as following packing sequences that consider crush resistance and item weight, are essential in reducing the risk of ingredient damage. Another common source of quality issues is placing similar-looking ingredients too close together, leading to mix-ups.
Our solution evaluates each item’s crush resistance, weight, and similarity to others, ensuring optimal placement of ingredients. This minimises packing errors by ensuring that the correct items are placed in the right packages and in the proper order. By considering crush resistance and weight, our solution ensures that more fragile, low-crush-resistance items are packed after heavier items, helping them remain intact throughout the packing and delivery process.
Enhanced Worker Safety
Adhering to workplace safety protocols, such as storing heavier crates on lower racks, is crucial for ensuring the health and safety of shop floor operatives. Additionally, creating bottlenecks where one worker is overloaded can lead to increased pressure and stress.
Our solution addresses these safety concerns by evenly distributing workload across stations and recipes, preventing any individual from being overloaded. It also considers item weight, placing heavy items that exceed an adjustable threshold on lower racks to minimise accidents and enhance worker safety.